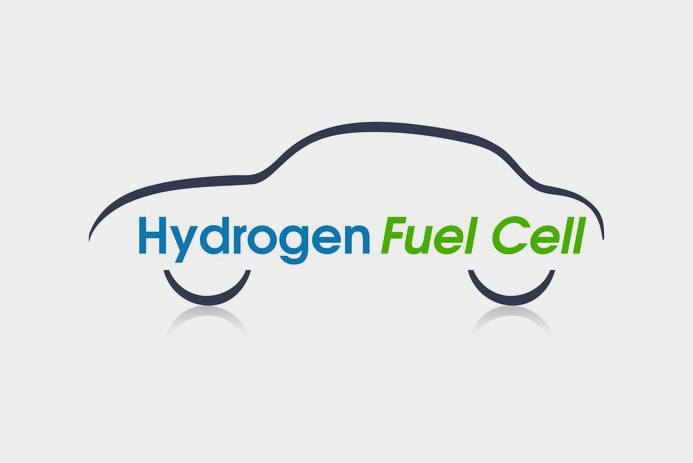
精确的压力测量在汽车燃料电池的早期起着至关重要的作用
虽然电动和混合动力车作为成熟的技术已经在广泛使用,但是在如何以安全,方便和低成本的方式存储电能,还有很大的进步空间。 作为昂贵蓄电池的潜在替代品,世界上大多数制造商正在研究利用氢气来发电以驱动电力牵引电动机。
使用质子交换膜(也称为聚合物电解质膜(PEM)燃料电池(PEMFC))的氢燃料电池已经在诸如Toyota’s Mirai的车辆中见到有限的批量生产。
燃料电池由夹在分离器之间的MEA(膜电极组件)组成。 MEA是施加有催化剂层的固体聚合物电解质膜。
这些电池通过氢和氧之间的化学反应产生电:氢和环境空气分别供应到燃料电池的阳极(负极)和阴极(正极)以发电。由于一个电池产生的电量小于一伏特,几百个电池串联连接以增加电压。 这种电池组合体被称为燃料电池堆。
此外,虽然小PEM燃料电池在正常空气压力下操作,但是10kW或更大的较大燃料电池通常在较高压力下操作。 在较高压力下操作的优点和缺点是复杂的,并且论点不是清楚的,双方具有许多令人信服的观点。
对氢燃料电池进行增压
与常规内燃机一样,增加燃料堆中的压力的目的是通过从相同尺寸的电池中提取更多的功率来增加比功率。 理想状态是压缩设备的额外成本、尺寸和重量将小于通过增加堆叠的尺寸来简单地获得额外功率的成本、尺寸和重量。
在ICE的情况下,优点明显超过缺点。 然而,对于燃料电池,优点和缺点也不过尔尔。 首先,这是因为在PEMFC的排出气体中几乎没有能量,并且任何压缩机必须大部分地或全部地使用由燃料电池产生的宝贵的电力来驱动。
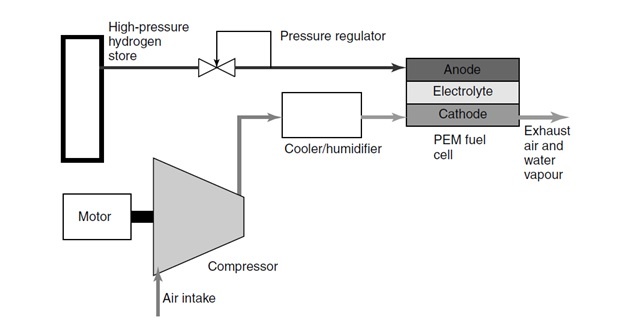
Image 1: 燃料电池图解
图片来源: James Larminie, Andrew Dicks (Fuel Cell Systems Explained)
最简单类型的加压PEM燃料电池是其中氢气来自高压汽缸的燃料电池。 在这种设计中,只有空气必须被压缩; 氢气从加压容器供给,因此其压缩“自由”。 这种将氢气供给到阳极的方法称为消音; 意味着没有气体的排放或循环 – 它完全被细胞消耗。
然而,用于空气的压缩机必须由电动机驱动,该电动机自然使用由燃料电池产生的一些有价值的电。 通常,对于100kW系统,功率消耗将为燃料电池功率的约20%。 如在ICE中,为了最佳效率,压缩空气还需要在进入PEM电池之前冷却。
平衡压力以优化性能
由于这是一种年轻的发展技术,如果要被广泛采用,这些“增压”燃料电池的可靠性和耐久性需要进行测试和开发,因此,正在进行大量的研究和开发以提高性能和寿命。
在受控条件下的测试是测试燃料电池的可行性和吸收的重要步骤。详细的测量数据作为输入信息是创建燃料电池运行模型的关键。然而,尽管有广泛的需求,合适的测量技术仍然仅处于正在开发的过程中。
通常,PEM燃料电池在接近环境至约3bar的压力和50至90℃的温度下操作。在较高的操作压力下实现高功率密度,但是由于压缩空气所需的功率,有效系统效率可能较低。较高的空气温度还增加功率密度,但是可能对水和热的管理造成巨大挑战,尤其是在较低的操作压力下。
因此,汽车PEM燃料电池系统的工作温度和压力的选择必须基于(a)高净系统效率,(b)小部件尺寸和(c)中性或正水平衡,使得车辆不必携带一个船上油库。
由于在较高压力下操作PEM燃料电池导致的功率增加主要是由于阴极激活过电压的减少的结果,因为增加的压力升高了交换电流密度,这具有提高开路电压(OCV ),如Nernst方程所述。
然而,如前所述,这种增压以增压燃料电池产生的功率为代价,因此,平衡压力到特定燃料电池的要求至关重要。与ICE增压压力一样,这只能通过使用经过精心校准到环境的高质量压力传感器进行精确的压力测量来完成。
然后将由STS提供的实验室级别传感器记录的这些压力测量值与燃料堆输出进行比较,以最小化寄生损失,同时优化电输出的增益。
随着汽车氢燃料电池技术的成熟和从真实世界试验收集的数据用于产生预测模型,工程师和研究人员无疑将更好地理解温度、压力和效率之间复杂的相互关系:但是在此期间这项研究将严重依赖于记录准确数据的高端传感器 。