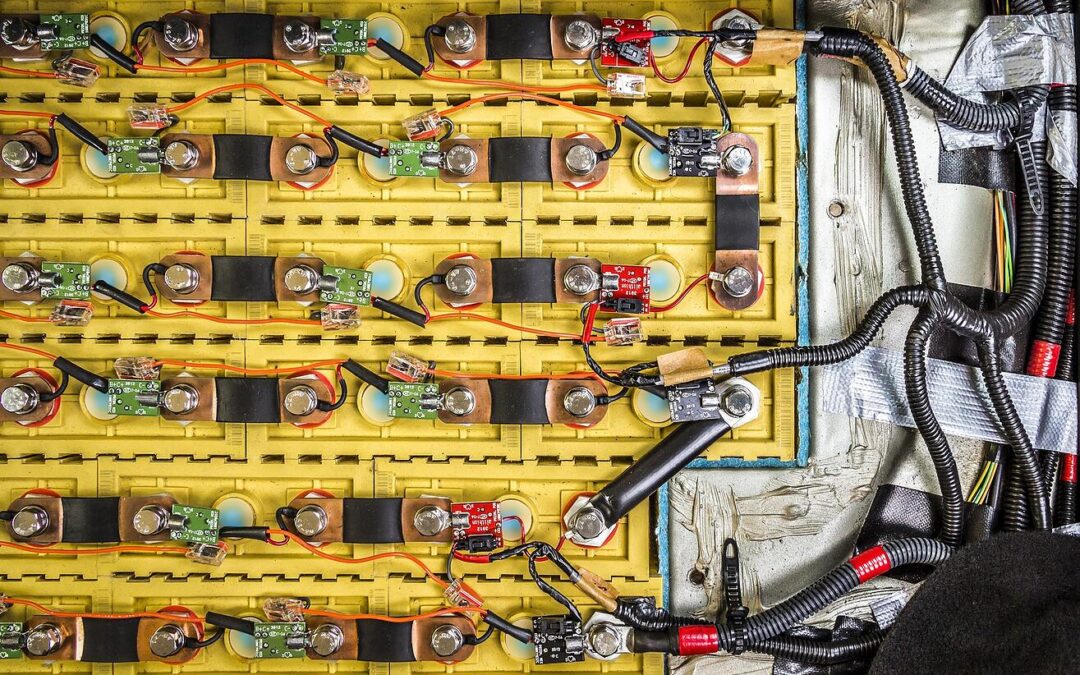
48V电气化助压发动机冷却系统
在2015年巴黎协定的背景下,该协议要求到2050年减少80%的温室气体排放,汽车行业正积极致力于发展“零排放”车辆。然而,在一个多世纪之后,内燃机不会在一夜之间突然消失,这让该行业别无选择只能探索新的技术来净化内燃机的排放。
尽管全面电气化是最终目标,但由于缺乏基础设施支持和大规模的推广,目前的技术成本过高。另一方面,混合动力车,特别是48伏轻型混合动力电动汽车,提供了一种成本效益高,易于实现的解决方案。
尽管48V轻型动力电车的技术实现相对简单,但它需要安装锂电池,以支持重启内燃机、制动能量回收和加速时的扭矩辅助。虽然这是一种非常有效的电力来源,但它也有几个缺点包括过热,可能导致“热失控”,甚至导致电池自燃。
热失控通常是由过量电流或环境温度过高引起的,并经过几个阶段的发展:
- 温度升高到80 ºC的时候,负极SEI膜开始分解,之后电解质与阳极发生反应。这种反应产生的热量会导致有机溶剂分解释放气体从而增加芯体内部的压力。
- 然而,由于缺氧,气体不会点燃。但是如果温度继续上升到135 ºC以上,分离器就会被溶解产生阳极和阴极之间的短路,导致金属氧化物阴极在200 ºC下分解,并释放出氧气致使电解液和氢气燃烧。
这是锂电池的特性,与全电动汽车一样,需要高效的电池管理和冷却系统 ,以确保安全、高效的操作。
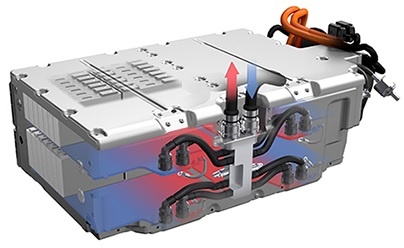
Image 1: 保时捷电池冷却系统 (图片来源: Charged EVs)
确定48V锂电池的冷却要求
为了调节高功率48V锂电池的电池组温度(超过1000Wh),制造商们开发了精密的电池热管理系统,这些系统通常包括流体冷却散热器,以确保热稳定性。
但是,在实施流体冷却散热器之前,在系统的多个位置确定并记录电池的温度和热通量是很重要的。这是用热电偶在电池的充放电循环中完成的。
一旦收集和分析了这些数据,趋势线就会根据热通量数据进行外推,然后在电荷和放电阶段为热通量曲线建立方程。
一旦整体趋势记录下来,就会使用诸如PTC Creo 3D这样的建模软件来创建一个“半散热器”模型。这样做的过程中,可以将流体流动通道的建议路径规划出来,从而在关键路径上创建所需的冷却通道。
有效的热传递需要通过散热器通道在流体的流量、压力和流体的温度之间保持一个良好的平衡。因此,优化进口和出口压力来控制通过散热器的冷却剂的流量是非常关键的。
热量平衡的压力测量关键
由于压力传感器的压力差在0.008273709bar被认为是最佳的,压力传感器用来测量通过散热器的流体压力,在不同的温度和压力下必须非常准确和稳定。
在这个关键的发展阶段,因为一贯的精确性和可靠的性能,制造商只依赖于固定的生产厂家提供的高质压力传感器。
集中于散热器,在这些测试中记录的测量数据被用来绘制在散热器内不同体积流量的最大和最小压力,允许不同的流量通道设计进行比较。
如伯努利方程所定义的,等高流动时,流速大,压力就小。
出于这个原因,工程师们选择了宽通道,低流量,并且尽可能越过电池,从而优化了从芯体到散热器的传热过程。
到目前为止,开发过程类似于在电动汽车电池测试中进行的,但是在48V 轻型混合动力车的情况下,电池冷却通常被集成到内燃机冷却系统中以降低成本和复杂性,从而增加了内燃机冷却系统的热负荷。因此,一旦电池冷却被优化工程师需要将散热器冷却系统集成到内燃机的冷却系统中。
在设计的这一阶段,开发团队不仅要监测通过散热器的任何压差,还要测量通过整个冷却系统的压降,以确保发动机冷却不会受到电池冷却的负面影响。
再次,工程师们在压力读数中寻找增量差异,重要的是用来记录这些值的压力传感器是稳定的,并且可重复结果。
因此,尽管48V的电池液态冷却系统集成到内燃机系统中增加了热负荷,但考虑周全的设计和开发,特别是在系统压力方面,显著提高了锂电池的安全可靠性和可循环性,而不影响发动机冷却装置。