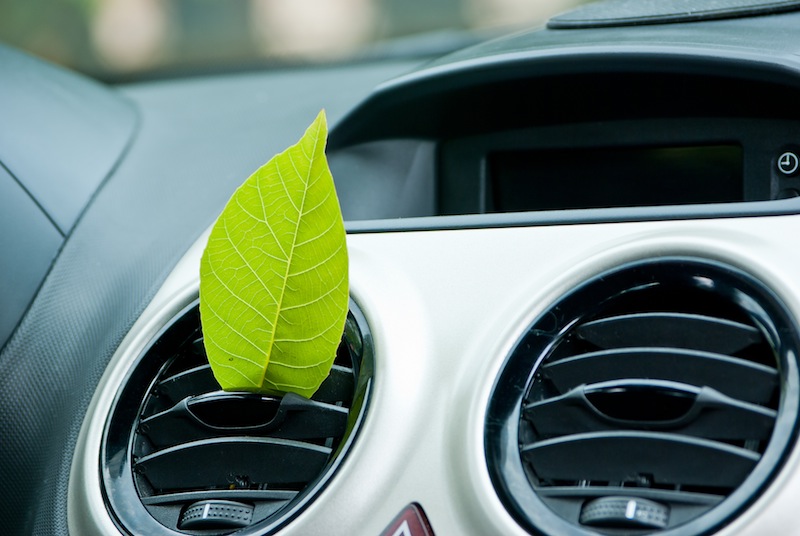
更小,更高效,更环保:车载二氧化碳空调
二氧化碳作为被公认的制冷剂已经有超过150年了。
事实上它现在才获准使用与车载空调是因为立法者施加了减少温室气体排放的压力,并改善了技术能力。这其中,压力测量在整个过程中发挥核心作用。
自2011年1月起,因为具有导致全球变暖的潜在影响,车载空调使用值高于150氟化温室气体已被欧盟指令禁止。在此期间,常见的四氟乙烷制混合冷剂(R134a)被替代使用。由于二氧化碳相比R134a对气候的破坏性少了1430倍,以及其本身的散热性能和良好的化学特性,因此也成为了一种不错的替代品。
关于二氧化碳作为冷凝剂的争论不能在被忽视。
- 作为一种自然产生的气体,它在全球享有无限的可用性和成本效益。
- 它的损害性要远远小于其他冷却剂,如R134a,R404A,R407C等。
- 根据工业副产品制造过程,它不需要昂贵的制造成本。
- 相对于其他新型制冷剂,它已经得到了很好的毒理学研究。
- 它既不具有毒性也不易燃,因此它比其他材料的危害风险要低很多。
- 它与所有其他常见的材料有很高的兼容性。
- 具有非常高的冷却性能,也适用于热泵。
但是从R134a转变到R744(是一种二氧化碳作为冷凝剂的缩写形式),并不是简简单单地就能实现。因为即使二氧化碳拥有众多的有点,但是也不能掩盖一些明显存在的缺点,这些缺点偶尔会在具有车载空调的车辆使用的情况下发生。一个非常高的工作压力环境和31℃的低临界温度要在这里强调。因此R744的转换必须通过汽车制造商和他们的供应商的测试实验台。
CO2空调-是如何运作的
一个普通的空气调节机的运转开始时,会激活车辆内的空调开关。其结果,压缩机的磁耦合被通电(尽管较新的压缩机没有磁耦合,是通过活塞行程内部压力调节)。滑轮和压缩机轴之间的连接就建立起来了,压缩机就开始制作制冷剂气体。现在通过这里的冷凝状态,气体被迫进入高压管道。在这个过程中,冷却剂的温度却在升高。内置在车辆的前端的冷凝器负责再次降低该温度。在该阶段中,制冷剂物理状态的变化从气态到液态。现在液体冷却剂被转移到接收机,其中所有的水分会被去除。接着,将冷却剂通过膨胀阀,制冷剂再次改变蒸发器内的物理状态。这一变化所需的能量从环境空气中提取,这反过来又降低了车辆内部中的温度拉伸。气态冷却剂现在可以由压缩机再次吸入,从而使循环重新开始。
这种冷却的方式针对R744也是相同的。唯一的区别是,该技术框架会有些变化。因为二氧化碳在系统中针对压力和温度会有其他要求。
相比于一个普通的的移动制冷系统,所附加的内热交换器具有极大的区别。因为使用CO2功能的空调的散热温度必须高于临界31°C。冷却循环如下进行:将气体冷凝到压缩机内的超临界压力。从那里它进入气体冷却器,区别于普通系统,它此时执行的是冷凝器的作用。这里是气体冷却,不会发生结露现象。进一步的冷却则发生在以下的热交换器中。在接下来的步骤中,CO 2是通过膨胀阀推压,将气体成蒸汽状态。接下来蒸气部分的会在蒸发器中被蒸发,其中冷却效果就发生在蒸发过程中。
除了内部热交换器和气体冷却器替换冷凝器,代表这套系统中的最核心的高压部分与移动制冷系统有着极大的区别。根据符合系统压力升高所有组件同时也要提升坚固性的要求,这种高压力尤其影响压缩机结构,因此压缩机需要重新按部就班的设计。
制造一个新的压缩机过程中,一个核心方向是通过非常小CO2分子来描述,因为它会很快通过通用的密封材料而扩散。因此一个全新用于防止冷却损失的密封方案的构想无可厚非,此密封件具有保护制冷剂的化学特性,并且能够承受高压力压缩机连续运转的功能 – 同时可以确定在试验台上进行长期测试。
甚至压缩机壳体本身无法简单地适用于从普通的冷却系统。在较长时期内有效地工作,它必须能够承受高温。波动性抽吸压力,这决定性的影响驱动器腔的压力,也代表了显著的挑战。在高压侧,极大值可以潜在达到200 bar的水平。由于这些特点,压缩机的泄漏将会比采用R134a的时候要快得多。相比几年前,一个更精确的生产组件可能,而今天现在这个问题是可以克服的。因此,对原型施工过程中压力的不断监测是势在必行。
利用二氧化碳与气候系统生产的高压已经超越了良好的环境属性和相对于R134a的更好的散热性。因为CO 2的高密度,所需要的安装空间相比较采用R134a冷却器甚至成效更好。对于相同的冷却性能,仅需要R134a制冷剂压缩机生产的13%体积流量。
对尺寸的不断减小也日益加强了的压力测量技术的使用情况。长期测试期间在特定 – 压阻式压力传感器,由于其小型化的能力,在低的压力和甚至在较高的压力范围其确切的结果高度精确的功能提供本身在这里。压阻式从STS压力传感器还为制造商提供开发新车型决定性的优势,这些仪器,由于其模块化结构,可以快速适应新的要求。