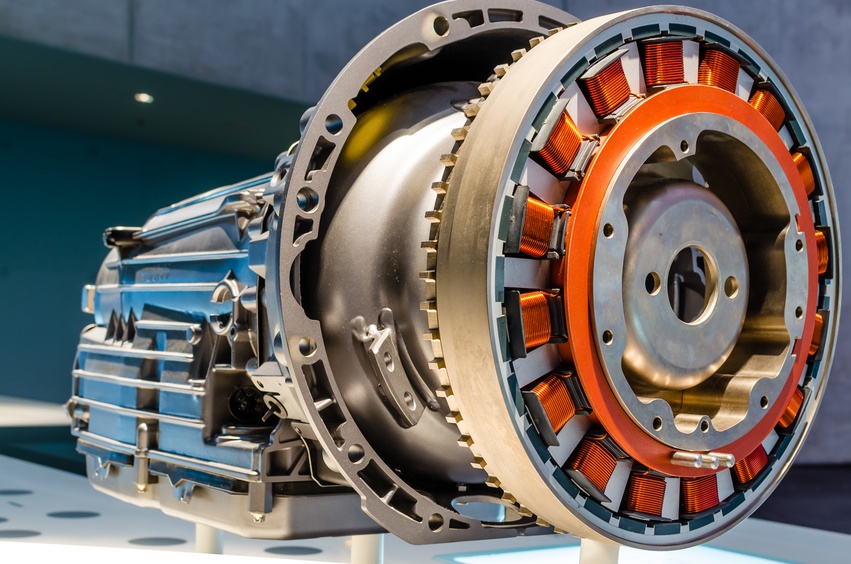
精确的压力测量是开发电动气油泵的关键
在全球排放目标不断升级的推动下,OEM厂商越来越多地转向电气化,以减少燃料消耗和温室气体排放。基于此由较小引擎驱动的混合动力汽车受到大众欢迎。
这些小型发动机的问题在于,动力消耗的辅助系统严重削弱了驾驶能力和性能。幸运的是,通过用电力驱动组件替换传统的机械部件,这些附加损失可以大大减少。正因为如此,电驱动泵正迅速地进入到一系列的生产中;尤其是驾驶驱动石油和水泵。
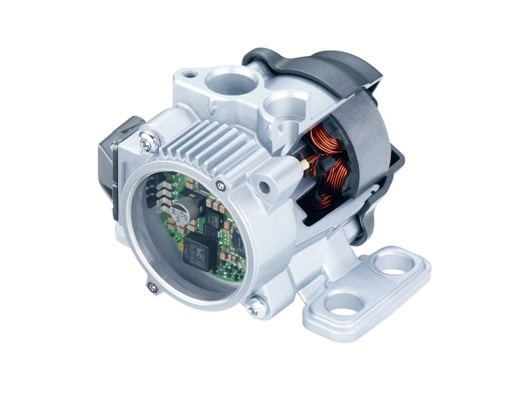
Image 1: 电动油泵示例 (图片来源: Rheinmetall Automotive)
但是,尽管这些好处显而易见,但在技术上很复杂,尤其是油泵:工程师不仅希望在特定的流量和压力下使石油流通,而且还希望能将之与发动机需求相匹配。
为了优化性能,很重要的一点是,通过小心地控制油流到不同的油循环分支来减少摩擦和泵气损失,并确保始终正常供压。
仿真依赖于精确的试验台油压和流量信息
一个电动油泵由三个子系统构成-泵、电机和电子控制器。因此,任何新应用开发的主要挑战是这些模块的高效集成,从而减少体积和重量以及组件的数量,同时优化性能。
油泵的主要功能是在最理想的压力下输送特定的油量。出于这个原因,他的设计是个迭代过程始于“泵齿轮”。对于大多数应用来说,泵的压力超过1到2巴,通常高达10巴。
正如在大多数引擎开发中一样,模拟和真实世界测试的结合可以加快设计的步伐。
回路设计开始于容积效率的初步评估并基于类似泵应用试验结果的收集。这些包含:泵速,油温,压力和流量。
用于评估的信息是准确的这一点很重要,因此数据收集必须使用高度可靠的精确测量设备能够在极端条件下在发动机内外提供精准读数。
为了确保精确性和可重复性,在测量压力时只采用最高质的传感器这点很重要。这些压力传感器不仅能在较大压力和温度跨度范围内提供可靠的数据,
并且他们还必须能够承受振动。
多年来,STS研发的压力传感器在发动机发展历程中能够满足OEM、一级供应商和专业发动机设计人员的需求。
开发一种比机械装置性能更出色的电动油泵
根据液压要求在不同流量、输出压力和油温所收集的信息,齿轮的初步设计最终确定。使用Matlab的模拟软件,关于物理系统行为的信息可以被合理地转化为一维代码。
在这一阶段,重要的是要注意,在特定压力下产生所需的流量,应该选择转速以促进电机和泵的最佳组合,而不会产生空穴或噪音问题:因此,标准的连续操作的速度范围通常在1500到3500转/分钟之间
接下来,使用LMS仿真软件生成几种设计 。这种仿真软件可以完善设计参数-在同时满足所有压力,流量和温度边界条件下的齿数和离心率。
在计算水力学的几何特性和过渡设计的最终确定后,在关键工作点驱动泵的总扭矩可以计算如下:
Mtot = MH + MCL + Mμ
一旦设计完成,工程样机就会在发动机测试台上进行评估。
油压、流量和温度再次在不同的发动机和泵速下进行测量,以验证通过模拟得到的结果。如果结果符合规格开发项目会最终确定,项目进入产业化阶段。
为了达到最佳的性能和耐久性,很明显所有的测量都是被精确记录的,但是压力传感器所产生的信息的重要性可能超过其他所有的数据——任何点上的压力不足都能导致灾难性故障。而超压浪费能源,并可能导致油封产生问题。